Solar thermal collector: Difference between revisions
m Reverted edits by 207.197.65.18 (talk) to last revision by Trusilver (HG) |
No edit summary |
||
Line 2: | Line 2: | ||
[[Image:Russiasolar.jpg|right|thumb|Solar Thermal Collector Dish]] |
[[Image:Russiasolar.jpg|right|thumb|Solar Thermal Collector Dish]] |
||
A '''solar thermal collector''' |
A '''solar thermal collector''' u9i=o0-k0iojmu9ij nbygb098uhj a [[solar collector]] designed to collect [[heat]] by [[Absorption (optics)|absorbing]] [[sunlight]]. The term is applied to [[solar hot water panel]]s, but may also be used to denote more complex installations such as solar parabolic, solar trough and solar towers or simpler installations such as [[solar air heat]]. The more complex collectors are generally used in [[solar power plant]]s where solar heat is used to generate [[electricity]] by heating water to produce steam which drives a [[turbine]] connected to an [[electrical generator]]. The simpler collectors are typically used for supplemental space heating in residential and commercial buildings. A collector is a device for converting the [[energy]] in solar radiation into a more usable or storable form. The energy in sunlight is in the form of [[electromagnetic radiation]] from the [[infrared]] (long) to the [[ultraviolet]] (short) wavelengths. The solar energy striking the Earth's surface depends on weather conditions, as well as location and orientation of the surface, but overall, it averages about 1,000 watts per square meter under clear skies with the surface directly perpendicular to the sun's rays. |
||
==Types of solar collectors for heat== |
==Types of solar collectors for heat== |
Revision as of 22:03, 18 October 2011
This article needs additional citations for verification. (July 2010) |
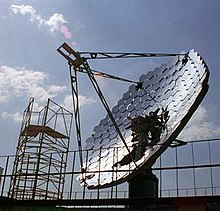
A solar thermal collector u9i=o0-k0iojmu9ij nbygb098uhj a solar collector designed to collect heat by absorbing sunlight. The term is applied to solar hot water panels, but may also be used to denote more complex installations such as solar parabolic, solar trough and solar towers or simpler installations such as solar air heat. The more complex collectors are generally used in solar power plants where solar heat is used to generate electricity by heating water to produce steam which drives a turbine connected to an electrical generator. The simpler collectors are typically used for supplemental space heating in residential and commercial buildings. A collector is a device for converting the energy in solar radiation into a more usable or storable form. The energy in sunlight is in the form of electromagnetic radiation from the infrared (long) to the ultraviolet (short) wavelengths. The solar energy striking the Earth's surface depends on weather conditions, as well as location and orientation of the surface, but overall, it averages about 1,000 watts per square meter under clear skies with the surface directly perpendicular to the sun's rays.
Types of solar collectors for heat
Solar collectors fall into two general categories: non-concentrating and concentrating. In the non-concentrating type, the collector area (i.e. the area that intercepts the solar radiation) is the same as the absorber area (i.e., the area absorbing the radiation). In these types the whole solar panel absorbs the light.
Flat plate and evacuated tube solar collectors are used to collect heat for space heating, domestic hot water or cooling with an absorption chiller.
Flat plate collectors

Flat plate collectors, developed by Hottel and Whillier in the 1950s, are the most common type. They consist of (1) a dark flat-plate absorber of solar energy, (2) a transparent cover that allows solar energy to pass through but reduces heat losses, (3) a heat-transport fluid (air, antifreeze or water) to remove heat from the absorber, and (4) a heat insulating backing. The absorber consists of a thin absorber sheet (of thermally stable polymers, aluminum, steel or copper, to which a matte black or selective coating is applied) often backed by a grid or coil of fluid tubing placed in an insulated casing with a glass or polycarbonate cover. In water heat panels, fluid is usually circulated through tubing to transfer heat from the absorber to an insulated water tank. This may be achieved directly or through a heat exchanger. Most air heat fabricates and some water heat manufacturers have a completely flooded absorber consisting of two sheets of metal which the fluid passes between. Because the heat exchange area is greater they may be marginally more efficient than traditional absorbers.[1]
There are a number of absorber piping configurations:
- harp — traditional design with bottom pipe risers and top collection pipe, used in low pressure thermosyphon and pumped systems
- serpentine — one continuous S that maximizes temperature but not total energy yield in variable flow systems, used in compact solar domestic hot water only systems (no space heating role)
- completely flooded absorber consisting of two sheets of metal stamped to produce a circulation zone. Because the heat exchange area is greater they may be marginally more efficient than traditional absorbers.
- boundary layer absorber collectors consisting of several layers of transparent an opaque sheets the enable absorption in a boundary layer. Because the solar energy is absorbed in the boundary layer, the heat conversion may be more efficient than for collectors where absorbed heat is conducted through a material before the heat is accumulated in a circulating liquid.[citation needed]
As an alternative to metal collectors, new polymer flat plate collectors are now being produced in Europe. These may be wholly polymer, or they may include metal plates in front of freeze-tolerant water channels made of silicone rubber. Polymers, being flexible and therefore freeze-tolerant, are able to contain plain water instead of antifreeze, so that they may be plumbed directly into existing water tanks instead of needing to use heat exchangers which lower efficiency. By dispensing with a heat exchanger in these flat plate panels, temperatures need not be quite so high for the circulation system to be switched on, so such direct circulation panels, whether polymer or otherwise, can be more efficient, particularly at low light levels.
Some early selectively coated polymer collectors suffered from overheating when insulated, as stagnation temperatures can exceed the melting point of the polymer.[2] [3] For example, the melting point of polypropylene is 160°C, while the stagnation temperature of insulated thermal collectors can exceed 180°C if control strategies are not used. For this reason polypropylene is not often used in glazed selectively coated solar collectors. Increasingly polymers such as high temperate silicones (which melt at over 250°C) are being used. Some non polypropylene polymer based glazed solar collectors are matte black coated rather than selectively coated to reduce the stagnation temperature to 150°C or less.
In areas where freezing is a possibility, freeze-tolerance (the capability to freeze repeatedly without cracking) can be delivered by the use of flexible polymers. Silicone rubber pipes have been used for this purpose in UK since 1999. Conventional metal collectors are vulnerable to damage from freezing, so if they are water filled they must be carefully plumbed so they completely drain down using gravity before freezing is expected, so that they do not crack. Many metal collectors are installed as part of a sealed heat exchanger system. Rather than having the potable water flow directly through the collectors, a mixture of water and antifreeze such as propylene glycol (which is used in the food industry) is used as a heat exchange fluid to protect against freeze damage down to a locally determined risk temperature that depends on the proportion of propylene glycol in the mixture. The use of glycol lowers the water's heat carrying capacity marginally, while the addition of an extra heat exchanger may lower system performance at low light levels.
A pool or unglazed collector is a simple form of flat-plate collector without a transparent cover. Typically polypropylene or EPDM rubber or silicone rubber is used as an absorber. Used for pool heating it can work quite well when the desired output temperature is near the ambient temperature (that is, when it is warm outside). As the ambient temperature gets cooler, these collectors become less effective.
Most flat plate collectors have a life expectancy of over 25 years.
Evacuated tube collectors
This section needs additional citations for verification. (August 2010) |

Most (if not all) vacuum tube collectors use heat pipes for their core instead of passing liquid directly through them. Evacuated heat pipe tubes (EHPTs) are composed of multiple evacuated glass tubes each containing an absorber plate fused to a heat pipe.[2] The heat from the hot end of the heat pipes is transferred to the transfer fluid (water or an antifreeze mix—typically propylene glycol) of a domestic hot water or hydronic space heating system in a heat exchanger called a "manifold". The manifold is wrapped in insulation and covered by a sheet metal or plastic case to protect it from the elements.
The vacuum that surrounds the outside of the tube greatly reduces convection and conduction heat loss to the outside, therefore achieving greater efficiency than flat-plate collectors, especially in colder conditions. This advantage is largely lost in warmer climates, except in those cases where very hot water is desirable, for example commercial process water. The high temperatures that can occur may require special system design to avoid or mitigate overheating conditions.

Some evacuated tubes (glass-metal) are made with one layer of glass that fuses to the heat pipe at the upper end and encloses the heat pipe and absorber in the vacuum. Others (glass-glass) are made with a double layer of glass fused together at one or both ends with a vacuum between the layers (like a vacuum bottle or flask) with the absorber and heat pipe contained at normal atmospheric pressure. Glass-glass tubes have a highly reliable vacuum seal but the two layers of glass reduce the light that reaches the absorber and there is some possibility that moisture will enter the non-evacuated area of the tube and cause absorber corrosion. Glass-metal tubes allow more light to reach the absorber and protect the absorber and heat pipe (contained in the vacuum) from corrosion even if they are made from dissimilar materials (see galvanic corrosion).
The gaps between the tubes may allow for snow to fall through the collector, minimizing the loss of production in some snowy conditions, though the lack of radiated heat from the tubes can also prevent effective shedding of accumulated snow.[3] [4]
Comparisons of flat plate and evacuated tube collectors
A long standing argument exists between protagonists of these two technologies. Some of this can be related to the physical structure of evacuated tube collectors which have a discontinuous absorbance area. An array of evacuated tubes on a roof has 1) open space between collector tubes and 2) (vacuum-filled) space occupied between the two concentric glass tubes of each collector tube. Consequently, a square meter of roof area covered with evacuated tubes (collector gross area) is larger than the area comprising the actual absorbers (absorber plate area). If evacuated tubes are compared with flat-plate collectors on the basis of area of roof occupied, a different conclusion might be reached than if the areas of absorber were compared. In addition, the way that the ISO 9806 standard [5] specifies the way in which the efficiency of solar thermal collectors should be measured is ambiguous, since these could be measured either in terms of gross area or in terms of absorber area. Unfortunately, power output is not given for thermal collectors as it is for PV panels. This makes it difficult for purchasers and engineers to make informed decisions.
![]() |
![]() |
A comparison of the energy output (kW.h/day) of a flat plate collector (blue lines; ThermoDynamics S42-P[dubious – discuss]; absorber 2.8 m2) and an evacuated tube collector (green lines; SunMaxx 20EVT[dubious – discuss]; absorber 3.1 m2. Data obtained from SRCC certification documents on the Internet.[dubious – discuss] Tm-Ta = temperature difference between water in the collector and the ambient temperature. Q = insolation during the measurements. Firstly, as (Tm-Ta) increases the flat plate collector loses efficiency more rapidly than the evac tube collector. This means the flat plate collector is less efficient in producing water higher than 25 degrees C above ambient (i.e. to the right of the red marks on the graph).[dubious – discuss] Secondly, even though the output of both collectors drop off strongly under cloudy conditions (low insolation), the evac tube collector yields significantly more energy under cloudiness than the flat plate collector. Although many factors obstruct the extrapolation from two collectors to two different technologies, above, the basic relationships between their efficiencies remain valid[dubious – discuss]. | A field trial[who?] illustrating the differences discussed in the figure on the left. A flat plate collector and a similar-sized evacuated tube collector were installed adjacently on a roof, each with a pump, controller and storage tank. Several variables were logged during a day with intermittent rain and cloud. Green line = solar irradiation. The top maroon line indicates the temperature of the evac tube collector for which cycling of the pump is much slower and even stopping for some 30 minutes during the cool parts of the day (irradiation low), indicating a slow rate of heat collection. The temperature of the flat plate collector fell significantly during the day (bottom purple line), but started cycling again later in the day when irradiation increased. The temperature in the water storage tank of the evac tube system (dark blue graph) increased by 8 degrees C during the day while that of the flat plate system (light blue graph) only remained constant. Courtesy ITS-solar[who?]. |
Flat-plate collectors usually lose more heat to the environment than evacuated tubes and this loss increases with temperature difference. So they are usually inappropriate choice of solar collector for high temperature commercial applications such as process steam production. Evacuated tube collectors have a lower absorber plate area to gross area ratio (typically 60-80% of gross area) compared to flat plates. (In early designs the absorber area only occupied about 50% of the collector panel. However this has changed as the technology has advanced to maximize the absorption area.) Based on absorber plate area, most evacuated tube systems are more efficient per square meter than equivalent flat plate systems. This makes them suitable where roof space is limiting, for example where the number of occupants of a building is higher than the number of square metres of suitable and available roof space. In general, per installed square metre, evacuated tubes deliver marginally more energy when the ambient temperature is low (e.g. during winter) or when the sky is overcast for long periods. However even in areas without much sunshine and solar heat, some low cost flat plate collectors can be more cost efficient than evacuated tube collectors. Although several European companies manufacture evacuated tube collectors, the evacuated tube market is dominated by manufacturers in the East. Several Chinese companies have long favorable track records of 15–30 years. There is no unambiguous evidence that the two collector technologies (flat-plate and evacuated tube) differ in long term reliability. However, the evacuated tube technology is younger and (especially for newer variants with sealed heat pipes) still need to prove equivalent lifetimes of equipment when compared to flat plates. The modularity of evacuated tubes can be advantageous in terms of extendability and maintenance, for example if the vacuum in one particular tube diminishes.

For a given absorber area, evacuated tubes can therefore maintain their efficiency over a wide range of ambient temperatures and heating requirements. In most climates, flat-plate collectors will generally be a more cost-effective solution than evacuated tubes. When employed in arrays, when considered instead on a per square metre basis, the efficient but costly evacuated tube collectors can have a net benefit in winter and also give real advantage in the summer months. They are well suited to cold ambient temperatures and work well in situations of consistently low sunshine, providing heat more consistently than flat plate collectors per square metre. On the other hand, heating of water by a medium to low amount (i.e. Tm-Ta) is much more efficiently performed by flat plate collectors. Domestic hot water frequently falls into this medium category. Glazed or unglazed flat collectors are the preferred devices for heating swimming pool water.[7] Unglazed collectors may be suitable in tropical or subtropical environments if domestic hot water needs to be heated by less than 20°C. A contour map can show which type is more effective (both thermal efficiency and energy/cost) for any geographic region.
Besides efficiency, there are other differences. EHPT's work as a thermal one-way valve due to their heat pipes. This also gives them an inherent maximum operating temperature which may be considered a safety feature. They have less aerodynamic drag, which may allow them to be laid onto the roof without being tied down. They can collect thermal radiation from the bottom in addition to the top. Tubes can be replaced individually without shutting down the entire system. There is no condensation or corrosion within the tubes. One hurdle to wider adoption of evacuated tube collectors in some markets is their inability to pass internal thermal shock tests where ISO 9806-2 section 9 class b is a requirement for durability certification.[8] This means that if unprotected evacuated tube collectors are exposed to full sun for too long prior to being filled with cold water the tubes may shatter due to the rapid temperature shift. There is also the question of vacuum leakage over their lifetime. Flat panels have been around much longer, and are less expensive. They may be easier to clean. Other properties, such as appearance and ease of installation are more subjective.
Air
Solar air heat collectors heat air directly, almost always for space heating. They are also used for pre-heating make-up air in commercial and industrial HVAC systems. They fall into two categories: Glazed and Unglazed.
Glazed systems have a transparent top sheet as well as insulated side and back panels to minimize heat loss to ambient air. The absorber plates in modern panels can have an absorptivity of more than 93%. Air typically passes along the front or back of the absorber plate while scrubbing heat directly from it. Heated air can then be distributed directly for applications such as space heating and drying or may be stored for later use.
Unglazed systems, or transpired air systems, consist of an absorber plate which air passes across or through as it scrubs heat from the absorber. These systems are typically used for pre-heating make-up air in commercial buildings.
These technologies are among the most efficient, dependable, and economical solar technologies available. Payback for glazed solar air heating panels can be less than 9–15 years depending on the fuel being replaced.
Bowl
This section needs additional citations for verification. (August 2011) |
A solar bowl is a type of solar thermal collector that operates similarly to a parabolic dish, but instead of using a tracking parabolic mirror with a fixed receiver, it has a fixed spherical mirror with a tracking receiver. This reduces its efficiency but makes it cheaper to build and operate. Designers call it a fixed mirror distributed focus solar power system. The main reason for its development was to eliminate the cost of moving a large mirror to track the sun as with parabolic dish systems.[9]
A fixed parabolic mirror creates a variously shaped image of the sun as it moves along the sky. Only when the mirror is pointed directly at the sun will the light focus in one point. That is why parabolic dish systems track the sun. A fixed spherical mirror focuses the light in the same place independent of the position of the sun. The light, however, is not directed to one point but is distributed on a line from the surface of the mirror to one half radius (along a line that runs through the sphere center and the sun).

As the sun moves across the sky, the aperture of any fixed collector changes. This causes changes in the amount of captured sunlight, producing what is called the sinus effect of power output. Proponents of the solar bowl design claim the reduction in overall power output compared with tracking parabolic mirrors is offset by lower system costs.[9]
The sunlight concentrated at the focal line of a spherical reflector is collected using a tracking receiver. This receiver is pivoted around the focal line and is usually counterbalanced. The receiver may consist of pipes carrying fluid for thermal transfer or photovoltaic cells for direct conversion of light to electricity.
The solar bowl design resulted from a project of the Electrical Engineering Department of the Texas Technical University, headed by Edwin O'Hair, to develop a 5 MWe power plant. A solar bowl was built for the town of Crosbyton, Texas as a pilot facility.[9] The bowl had a diameter of 65 ft (20 m), tilted at a 15° angle to optimize the cost/yield relation (33° would have maximized yield). The rim of the hemisphere was "trimmed" to 60°, creating a maximum aperture of 3,318 square feet (308.3 m2). This pilot bowl produced electricity at a rate of 10 kW peak.[citation needed]
A 15-meter diameter Auroville solar bowl was developed from an earlier test of a 3.5-meter bowl in 1979–1982 by the Tata Energy Research Institute. That test showed the use of the solar bowl in the production of steam for cooking. The full-scale project to build a solar bowl and kitchen ran from 1996, being fully operational by 2001.[citation needed]
Types of solar collectors for electricity generation
Parabolic troughs, dishes and towers described in this section are used almost exclusively in solar power generating stations or for research purposes. Although simple, these solar concentrators are quite far from the theoretical maximum concentration.[10][11] For example, the parabolic trough concentration is about 1/3 of the theoretical maximum for the same acceptance angle, that is, for the same overall tolerances for the system. Approaching the theoretical maximum may be achieved by using more elaborate concentrators based on nonimaging optics.
Parabolic trough

This type of collector is generally used in solar power plants. A trough-shaped parabolic reflector is used to concentrate sunlight on an insulated tube (Dewar tube) or heat pipe, placed at the focal point, containing coolant which transfers heat from the collectors to the boilers in the power station.
Parabolic dish

It is the most powerful type of collector which concentrates sunlight at a single, focal point, via one or more parabolic dishes—arranged in a similar fashion to a reflecting telescope focuses starlight, or a dish antenna focuses radio waves. This geometry may be used in solar furnaces and solar power plants.
There are two key phenomena to understand in order to comprehend the design of a parabolic dish. One is that the shape of a parabola is defined such that incoming rays which are parallel to the dish's axis will be reflected toward the focus, no matter where on the dish they arrive. The second key is that the light rays from the sun arriving at the Earth's surface are almost completely parallel. So if the dish can be aligned with its axis pointing at the sun, almost all of the incoming radiation will be reflected towards the focal point of the dish—most losses are due to imperfections in the parabolic shape and imperfect reflection.
Losses due to atmosphere between the dish and its focal point are minimal, as the dish is generally designed specifically to be small enough that this factor is insignificant on a clear, sunny day. Compare this though with some other designs, and you will see that this could be an important factor, and if the local weather is hazy, or foggy, it may reduce the efficiency of a parabolic dish significantly.
In dish stirling power plant designs, a stirling engine coupled to a dynamo, is placed at the focus of the dish, which absorbs the heat of the incident solar radiation, and converts it into electricity.
Power tower

A power tower is a large tower surrounded by tracking mirrors called heliostats. These mirrors align themselves and focus sunlight on the receiver at the top of tower, collected heat is transferred to a power station below.
Advantages
- Very high temperatures reached. High temperatures are suitable for electricity generation using conventional methods like steam turbine or some direct high temperature chemical reaction.[citation needed]
- Good efficiency. By concentrating sunlight current systems can get better efficiency than simple solar cells.
- A larger area can be covered by using relatively inexpensive mirrors rather than using expensive solar cells.
- Concentrated light can be redirected to a suitable location via optical fiber cable. For example illuminating buildings.
- Heat storage for power production during cloudy and overnight conditions can be accomplished, often by underground tank storage of heated fluids. Molten salts have been used to good effect.
Disadvantages
- Concentrating systems require sun tracking to maintain Sunlight focus at the collector.
- Inability to provide power in diffused light conditions. Solar Cells are able to provide some output even if the sky becomes a little bit cloudy, but power output from concentrating systems drop drastically in cloudy conditions as diffused light cannot be concentrated passively.
Standards
- http://www.iso.org/iso/catalogue_detail.htm?csnumber=17678: Test methods for solar collectors.
- EN 12975: Thermal solar systems and components. Solar collectors.
- EN 12976: Thermal solar systems and components. Factory made systems.
- EN 12977: Thermal solar systems and components. Custom made systems.
- Solar Keymark: Thermal solar systems and components. Higher level EN 1297X series certification which includes factory visits.
See also
- Concentrated solar power
- Solar hot water
- Solar thermal energy
- Insulated glazing
- Selective surface
- Solar air heat
- Solar oven
- Solar heating
- Solar Flower Tower
- Seasonal thermal store
- Trombe wall
- Zeolite
- List of solar thermal power stations
References
- ^ rise.org.au. "Domestic Hot Water Systems". Retrieved 2008-10-29.
- ^ Vacuum Tube Liquid-Vapor (Heat-Pipe) Collectors
- ^ Solar Flat Plate vs. Evacuated Tube Collectors
- ^ Trinkl, Christoph (2005-06-21). "Performance of Vacuum Tube and Flat Plate Collectors Concerning Domestic Hot Water Preparation and Room Heating" (PDF). 2nd European Solar Thermal Energy Conference 2005 (estec2005). CENTRE OF EXCELLENCE FOR SOLAR ENGINEERING at Ingolstadt University of Applied Sciences. Retrieved 2010-08-25.
{{cite conference}}
: Unknown parameter|booktitle=
ignored (|book-title=
suggested) (help); Unknown parameter|coauthors=
ignored (|author=
suggested) (help) - ^ ISO 9806-2:1995. Test methods for solar collectors -- Part 2: Qualification test procedures. International Organization for Standardization, Geneva, Switzerland
- ^ Tom Lane. Solar Hot Water Systems: Lessons Learned, 1977 to Today. p. 5.
- ^ Flatplate vs. EHTP
- ^ FSEC test standard 102-10 section 5.6. [1]
- ^ a b c Calhoun, Fryor "Duel for the Sun" Texas Monthly November 1983
- ^ Julio Chaves, Introduction to Nonimaging Optics, CRC Press, 2008 [ISBN 978-1420054293]
- ^ Roland Winston et al.,, Nonimaging Optics, Academic Press, 2004 [ISBN 978-0127597515]
External links
- Canadian government ratings of solar collectors
- Parabolic Light Collector
- U.S. ratings of solar thermal collectors, updated regularly—flat plate, evacuated, air and pool collectors rated
- Panorama showed the pervasive usage of solar heater in Hawaii islands
- Auroville Solar Bowl
- Crosbyton Inventory of Records
- Solar Bowl Information
- Feasibility of photovoltaic Cells on a Fixed Mirror Distributed Focus Solar Bowl