5S (methodology): Difference between revisions
m deleted 'and', 559010490 14.97.171.205 (talk) |
|||
Line 6: | Line 6: | ||
There are five primary 5S phases: sorting, set in order, systematic cleaning, standardizing, and sustaining. |
There are five primary 5S phases: sorting, set in order, systematic cleaning, standardizing, and sustaining. |
||
=== |
===So=== |
||
Eliminate all unnecessary tools, parts. Go through all tools, materials, and so forth in the plant and work area. Keep only essential items and eliminate what is not required, prioritizing things per requirements and keeping them in easily-accessible places. Everything else is stored or discarded. |
Eliminate all unnecessary tools, parts. Go through all tools, materials, and so forth in the plant and work area. Keep only essential items and eliminate what is not required, prioritizing things per requirements and keeping them in easily-accessible places. Everything else is stored or discarded. |
||
Revision as of 13:04, 13 June 2013
This article needs additional citations for verification. (May 2011) |

5S is the name of a workplace organization method that uses a list of five Japanese words: seiri, seiton, seiso, seiketsu, and shitsuke. Transliterated or translated into English, they all start with the letter "S". The list describes how to organize a work space for efficiency and effectiveness by identifying and storing the items used, maintaining the area and items, and sustaining the new order. The decision-making process usually comes from a dialogue about standardization, which builds understanding among employees of how they should do the work.
The 5 S's
There are five primary 5S phases: sorting, set in order, systematic cleaning, standardizing, and sustaining.
So
Eliminate all unnecessary tools, parts. Go through all tools, materials, and so forth in the plant and work area. Keep only essential items and eliminate what is not required, prioritizing things per requirements and keeping them in easily-accessible places. Everything else is stored or discarded.
Straightening or Setting in Order to Flow
Arrange the work, workers, equipment, parts, and instructions in such a way that the work flows free of waste through the value added tasks with a division of labour necessary to meet demand. This is by far the most misunderstood and incorrectly applied S and has been responsible for many lean transformations failing to produce the benefits expected. When applied correctly with flow established this step eliminates the majority of the non-value-added time and allows the rest of the zero defect philosophy to be enabled. Put simply until you have an orderly flow you cannot have an orderly flow of problems to solve and the notion of zero defects is impossible.
Systematic Cleaning (Shine)
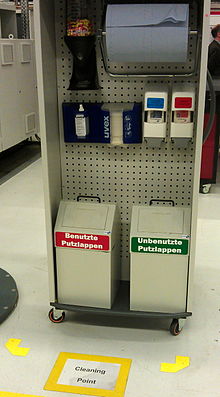
Clean the workspace and all equipment, and keep it clean, tidy and organized. At the end of each shift, clean the work area and be sure everything is restored to its place. This step ensures that the workstation is ready for the next user and that order is sustained.
Standardize
Ensure uniform procedures and setups throughout the operation to promote interchangeability.
Service (Sustain)
Ensure disciplined adherence to rules and procedures to prevent backsliding.
Additional S's
Three other phases are sometimes included: safety, security, and satisfaction. This is however not a traditional set of "phases". Safety for example is inherent in the 5S methodology and is not a step in itself. Therefore the additions of the phases are simply to clarify the benefits of 5S and not a different or more inclusive methodology.
Safety
A sixth phase, "Safety", is sometimes added.[1] There is debate over whether including this sixth "S" promotes safety by stating this value explicitly, or if a comprehensive safety program is undermined when it is relegated to a single item in an efficiency-focused business methodology.
Security
A seventh phase, "Security", can also be added.[citation needed] To leverage security as an investment rather than an expense, the seventh "S" identifies and addresses risks to key business categories including fixed assets (PP&E), material, human capital, brand equity, intellectual property, information technology, assets-in-transit and the extended supply chain.
Satisfaction
An eighth phase, "Satisfaction", can be included. [citation needed] Employee Satisfaction and engagement in continuous improvement activities ensures the improvements will be sustained and improved upon. The Eighth waste – Non Utilized Intellect, Talent, and Resources can be the most damaging waste of all.
It is important to have continuous education about maintaining standards.[citation needed] When there are changes that affect the 5S program such as new equipment, new products or new work rules, it is essential to make changes in the standards and provide training. Companies embracing 5S often use posters and signs as a way of educating employees and maintaining standards.
The Origins of 5S
5S was developed in Japan. It was first heard of as one of the techniques that enabled what was then termed 'Just in Time Manufacturing'. The Massachusetts Institute of Technology's 5-year study into the future of the automobile in the late 1980s[2] identified that the term was inappropriate since the Japanese success was built upon far more than components arriving only at the time of requirement. John Krafcik, a researcher on the project, ascribed Lean to the collective techniques being used in Japanese automobile manufacturing; it reflected the focus on waste in all its forms that was central to the Japanese approach. Minimised inventory was only one aspect of performance levels in companies such as Toyota[3] and in itself only arose from progress in fields such as quality assurance and Andon boards to highlight problems for immediate action.
5S was developed by Hiroyuki Hirano within his overall approach to production systems.[4] Many Western managers coming across the approach for the first time found the experience one of enlightenment. They had perhaps always known the role of housekeeping within optimized manufacturing performance and had always known the elements of best practice. However, Hirano provided a structure for improvement programs. He pointed out a series of identifiable steps, each building on its predecessor. Western managers, for example, had always recognized the need to decide upon locations for materials and tools and upon the flow of work through a work area; central to this (but perhaps implicit) is the principle that items not essential to the process should be removed – stored elsewhere or eliminated completely. By differentiating between Seiri and Seiton, Hirano made the distinction explicit. He taught his audience that any effort to consider layout and flow before the removal of the unnecessary items was likely to lead to a sub-optimal solution.
Equally the Seiso, or cleanliness, phase is a distinct element of the change program that can transform a process area. Hirano's view is that the definition of a cleaning methodology (Seiso) is a discrete activity, not to be confused with the organisation of the workplace, and this helps to structure any improvement program. It has to be recognised, however, that there is inevitably an overlap between Seiton and Seiso. Western managers understood that the opportunities for various cleanliness methodologies vary with the layout and storage mechanisms adopted. However, breaking down the improvement activity in this way clarifies that the requirements for the cleanliness regime must be understood as a factor in the design aspect of Seiton. As noted by John Bicheno,[5] Toyota's adoption of the Hirano approach, is '4S', with Seiton and Seiso combined – presumably for this very reason. The improvement team must avoid the trap of designing the work area and then considering the cleanliness or tidiness mechanism.
Hirano also reminded the world of the Hawthorne effect. We can all introduce change and while people in the business consider the change program to be under management focus the benefits of the change will continue, but when this focus has moved (as is inevitably the case) performance once more slips. Western managers, in particular, may have benefited from the distinction between the procedural or mechanical elements, Seiketsu, of keeping these matters in focus and the culture change, Shitsuke, which is a distinct approach to bringing about a new way of working. A number of publications on the subject in the West have questioned whether this culture can really be tackled as part of an exercise of relatively limited scope.[6] The broader kaizen, or continuous improvement, approach is built, among other things, upon the company's valuation of all members of the workforce. If employees don't feel valued within the overall company culture, perhaps the change required falls outside the limits of a housekeeping improvement program.
See also
References
- ^ "Lean and Environment Training Modules" (PDF). United States Government, Green Supply Network. Retrieved 12 July 2012.
- ^ Womack, James; Jones, Daniel; Roos, Daniel (1991). Machine That Changed The World. Productivity Press. ISBN 978-1-84737-055-6.
- ^ Ohno, Taiichi. Toyota Production System (TPS). ISBN 978-0915299140.
- ^ Hirano, Hiroyuki (1995). 5 Pillars of the Visual Workplace. Cambridge, MA: Productivity Press. ISBN 978-1-56327-047-5.
- ^ Bicheno, John. New Lean Toolbox: Towards Fast, Flexible Flow. Buckingham: PICSIE. ISBN 978-0-9541244-1-0.
- ^ 5S - The Housekeeping Approach Within Lean, Ian Henderson